How Industrial Automation is Revolutionizing Field Service Management
.webp?updatedAt=1750934493882)
Field service isn’t what it used to be. Gone are the days of assumption-based decisions and paper checklists. Thanks to digital transformation and a wave of automation, the industry has had a serious glow-up.
As tech gets smarter, companies in management, monitoring, and maintenance are ditching the duct tape and spreadsheets in favor of practical, data-backed tools.
At the heart of this change is industrial automation software, machines, and smart devices working together to handle both routine and complex tasks.
What does this look like in the real world?
- Online systems that flag problems before your technician even rolls out
- Scalable platforms like Allen Bradley’s ControlLogix PLC, the go-to for teams who need flexible growth
- Modular expansion so your system grows without adding unplanned downtime
And it’s not just the tools evolving.
Technicians' workflows, equipment upkeep, and customer expectations are all moving into a smarter, faster future.
.webp?updatedAt=1750935131413)
Real-Time Monitoring Is Now a Must-Have
Nobody wants to play catch-up when something breaks. Real-time monitoring helps teams stay ahead of issues instead of reacting after the fact.
Think of it as giving your equipment a voice and your team the ability to respond in real time.
Ready to get started with Field Promax?
Sign Up FreeWhat this means in the field:
- Anomaly detection: Spot unusual behavior early before it causes downtime
- Remote access: Get alerts and system updates from anywhere without extra site visits
- Central dashboards: See what’s happening across locations in one place
- Asset comparisons: Identify performance gaps between machines
- Faster resolution: Shorter repair times, higher uptime, and less stress for the team
Making Informed Decisions That Are Backed by Data
Automation is doing more than speeding things up. It’s putting useful data into the hands of field managers. With real numbers and clear trends, teams are no longer relying on assumptions or gut feelings.
Now, managers can:
- Review past service patterns
- Spot common trouble areas
- Adjust schedules before problems stack up
Many businesses turn to automation hardware when they need structured data to back up high-stakes decisions. This data-driven shift does something else, too: it builds a culture of continuous improvement. When facts drive choices, teams get better without second thoughts.
Better yet:
Smart data analysis can catch things that humans often overlook, like early signs of wear or low-key energy waste. That means more precise fixes, fewer breakdowns, and money saved in the long run.
Predictive Maintenance: No More Fixing in Panic Mode
Why wait for something to break if you can prevent it?
Predictive maintenance is helping field service teams do just that: fix things before they cause chaos.
Automated systems feed real-time performance data into tools that track equipment health. That way, teams know when a part is starting to wear out and can replace it before it fails.
This approach leads to:
- Less downtime
- Fewer emergency call-outs
- Longer equipment life
- Lower repair costs over time
Most importantly, it allows companies to ditch rigid maintenance calendars. Instead of following a fixed plan, they work on a condition-based schedule, servicing equipment only when needed. It’s more efficient, more affordable, and doesn’t compromise reliability.
Troubleshooting Without the Site Visit
Gone are the days of blindly showing up to figure out what went wrong. With automation in play, remote diagnostics now give technicians a clear view of the issue before they arrive.
In many cases:
- Problems can be fixed remotely
- Techs show up fully prepared with the right tools and parts.
- Service teams avoid unnecessary trips altogether
It also helps prioritize tasks better, emergencies get attention fast, while minor glitches can be handled without dispatching a crew.
Remote diagnostics let senior techs guide field staff in real time using shared screens or live diagnostics tools, helping validate fixes instantly and keeping service moving without delay.
Smarter Scheduling for Field Teams
Coordinating field teams is no small task. But automation has made it a whole lot smarter.
Scheduling software now matches the right tech to the right job based on:
- Skill level
- Location
- Priorities of the task
That means fewer delays, less back-and-forth, and a big cut in fuel and idle time.
When last-minute changes come up, cancellations, urgent orders, or reroutes, the system adjusts on the fly. Customers get instant updates, techs avoid burnout, and companies keep their calendars running smoothly without overbooking or underperforming.
Safer Worksites, Built-In Compliance
Automation doesn’t just make things faster, it makes them safer too. Smart systems monitor conditions and send out alerts before a risky situation becomes a serious one.
Whether it’s a sudden spike in temperature, a voltage irregularity, or signs of equipment failure, early warnings help crews step in before things get out of hand.
On the compliance side:
- Service logs and reports are auto-generated
- Documentation is consistent, time-stamped, and audit-ready
- Real-time alerts support safety protocols like system shutoffs or pre-check inspections.
In short, fewer hazards, better documentation, and a safer, more controlled environment for everyone on the ground.
Want a personalized demo?
See how Field Promax can transform your field operations
1. Onboarding That Doesn’t Take Forever
Getting new hires up to speed used to mean long manuals and longer shadowing sessions. Not anymore.
Today’s systems offer:
- Step-by-step, in-app guidance
- Built-in training modules
- Hands-on practice without the risk
Some teams even use augmented reality simulations to train techs in real scenarios without hazards or pressure.
Automation also keeps track of how each person is doing. It spots skill gaps early so managers can give support where it’s needed most. Over time, this builds a valuable training record that helps shape better programs in the future.
2. Easier Communication, Stronger Teams
Field teams are often spread out. Automation tools help them stay connected and on the same page.
Real-time checklists, shared dashboards, and mobile updates mean:
- Everyone sees the same info
- Back office and field teams sync up
- Errors drop, and response times improve
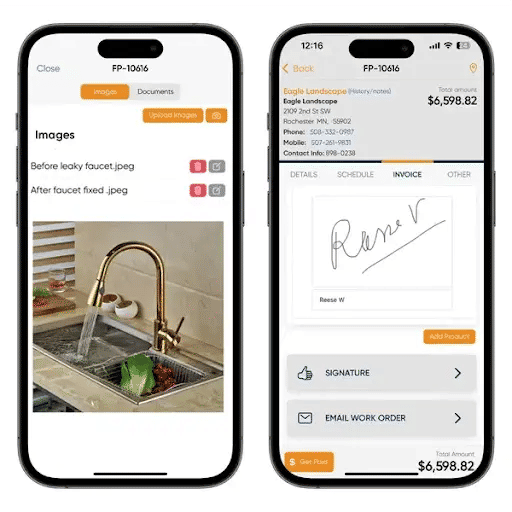
It also helps customer service teams stay in the loop, so updates reach the customer quickly. With smoother teamwork and fewer hold-ups, customers get a response fast, and techs spend less time chasing information.
3. Happier Customers, Fewer Follow-Ups
Automation makes life easier for your team, but the real win is what it does for your customers.
Thanks to things like:
- On-time reminders
- Technician tracking
- Easy follow-up verification
Customers stay informed and confident in the service. They don’t need to call twice to check the status or wonder who’s showing up. Everything is clear and consistent.
Timely updates, accurate ETAs, and fewer surprises lead to better reviews and long-term loyalty.
.webp?updatedAt=1750935131082)
4. Data-Driven Service That Works
Tools powered by machine learning and automation are making a difference in the field.
Here’s how they help:
- Flag critical issues based on sensor data
- Suggest repair options based on history
- Smart assistants help streamline support without delays
It’s not about replacing techs, it’s about giving them better information to work with and cutting down time spent troubleshooting.
5. Using the Right Parts Still Matters
Automation only works well when the hardware behind it is up to the task.
That means:
- Controllers and modules must be compatible
- Communication systems must align
- Sensors must deliver reliable data in real time
Upgrading older infrastructure? Reliable systems like the Allen Bradley ControlLogix PLC are helping teams record and respond to live data effectively, a key part of making predictive maintenance work.
Final Thoughts: Automation Isn’t the Future, It’s the Standard
What used to sound futuristic is now an everyday reality. Automation has become essential in field service, not just for speed, but for accuracy, safety, and better decision-making.
From smarter scheduling to real-time insights and predictive repairs, teams that adopt automation are ready to face demand, manage change, and deliver consistent service at scale.
For more information, contact Field Promax
We're here to help you get started